1、輸送帶在運行中存在的磨損形式
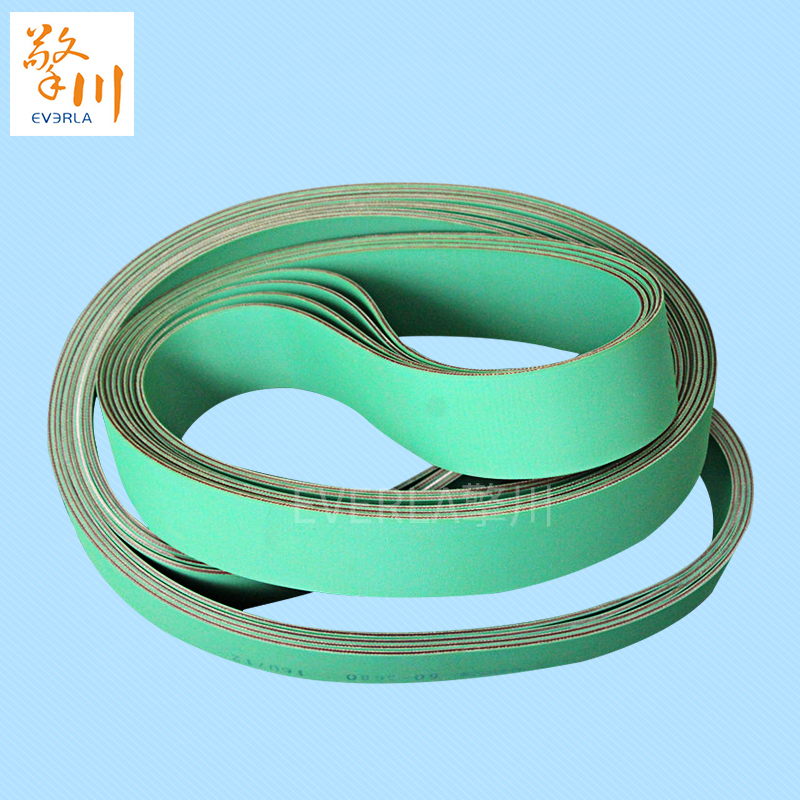
輸送帶更換的主要原因是磨損,磨損一般分為以下3種形式:
1)輸送帶的硫化接頭處磨損通常是由于輸送帶自身材料要比硫化接頭處膠層的耐磨度高或熱硫化質量問題,造成硫化接頭膠層局部磨損,露出鋼絲芯或尼龍芯,對輸送帶之間的硫化接頭強度構成嚴重威脅。
2)輸送帶在裙板部位磨損
由于輸送帶導料裝置的裙板調整不當或者導料裙板設計不良,會導致裙板在運行中磨損輸送帶,造成輸送帶兩側上膠層磨損嚴重,整條膠帶縱向運行方向露出鋼繩芯或尼龍芯,一旦鋼繩芯翹起,極易纏繞到托輥上,造成鋼絲帶脫絲或膠帶的撕裂。
3)輸送帶中間部位磨損這是由落料沖擊造成的,由于漏斗的落料點相對固定,因此輸送帶承受沖擊的部位磨損加劇,造成輸送帶沿運行方向局部磨損嚴重,也會導致露出的鋼繩芯脫絲或輸送帶撕裂。對于尼龍膠帶則造成中間部位強度下降,由于承載托輥存在3?!?。的前傾角,所以在承載托輥趨中力的作用下,膠帶運行中會出現“疊帶”的危險現象。
2.輸送帶磨損的處理方式
上述的磨損形式均對輸送機的正常運行構成嚴重的威脅,但僅僅因為輸送帶局部強度的降低或者局部磨損就對其進行更換,則運行成本將會大大提高,因此,在實際運行中,采用下列措施進行局部維修。
1)局部熱硫化技術采用硫化機進行熱硫化,對于接頭局部磨損的部位,采用熱硫化技術能恢復輸送帶的性能,效果較好。缺點是人力物力投入較大,時間也較長,適合于小于硫化板表面積的局部處理,對于大面積磨損的處理難度非常大。
2)局部冷硫化技術對磨損部位打磨處理后,將冷硫化膠按比例調和后均勻涂到膠帶磨損的表面,能基本恢復輸送帶性能。但固化時間較長,常溫固化約10~24h,表面處理也不光滑,清掃器投入后,清掃效果不好。
3)局部冷粘技術一般采用德國蒂普拓普公
司修補條(縱向裂口)。優(yōu)點是人力物力投入較少,具有較好的耐磨損和補強性能,恢復時間較短;缺點是對環(huán)境的要求高,不能恢復到原輸送帶表面平整要求,清掃器清掃效果不好。但是對于高利用率的設備,冷粘技術的推廣應用有效地緩解了硫化技術的局限性帶來的設備壓力。